From Traditional Braiding Methods to Additive Manufacturing for Fabricating Mckibben Artificial Muscles
Introduction
Mckibben artificial muscles [1-5] are of interest because of their practical engineering performances such as large contraction strains, high blocked forces and short response time. Since these performances are comparable to those of biological muscles, the demand for employing these muscles for robotic tools and medical devices is high. Mckibben artificial muscles are simply made of three essential parts: an inner elastomeric bladder, a braided sleeve and the fluid supply system [6]. The inner elastomeric bladder is surrounded by a braided sleeve which is connected to the fluid supply system. To activate the muscle, pressurized fluid is normally injected into the one end sealed inner bladder, once the inner bladder is fully pressurized, the volume of the inner bladder increases, and it produces force in radius direction against the braided sleeve. The braided sleeve subsequently transforms the generated radius force into the length direction along the braid axis [4]. The muscle, therefore, generates a length change or tensile blocked force depending on the experimental conditions. The magnitude of the generated force and length change significantly rely on the topology and mechanical properties of the braided sleeve. Previous literature described that the generated tensile blocked force normally decreases remarkably with increasing the initial angle of the braided sleeve up to the critical angle of 54.44 for a fixed input pressure. The amount of contraction strain also depends on the initial angle of the braided sleeve and for ideal systems is independent of internal pressure [3,7]. The amount of contraction strain usually declines with increasing initial braid angle and reaches zero contraction strain at the critical angle. Given the importance of the braided sleeve design to the performance of McKibben artificial muscles, here we review the trend of leading methods for manufacturing braided sleeves used in McKibben muscles and also suggest some design strategies for the future manufacturing.
Traditional Braided Sleeves
A braided sleeve is basically manufactured with several yarns interwoven with each other and fabricated around a mandrel [8,9]. There are important geometric variables that affect the final mechanical performance of the braided sleeve with an assumption that the braid is made of flat strip yarn. These variables include the braid angle, α, helical length. L, of one pitch of yarn, mandrel or braid diameter, db, yarn width, wy, and cover factor, C as shown in Figure 1. The cover actor is an essential property of the braid and is defined as the ratio of area occupied by yarn within a periodic pore unit to the total area of the pore unit, as shown in Figure 1. As derived by Zhang et al. [8], the cover factor is described by equation (1) and is a function of braid diameter, initial braid angle, yarn width, and the number of threads, Nc. Braided sleeves with the high cover factors are normally required in manufacturing McKibben artificial muscles due to the working conditions at high pressures. When fewer fibers are used in manufacturing of the braided sleeve this results in wider gaps between the fibers and consequently may result in muscle rupturing due to the internal bladder passing through the gaps at high pressures. Figure 2 illustrates the three different types of the braided sleeve with different cover factors.
Figure 1: Braided sleeve geometry (A) braided tube (B) Braid geometry of a helically slit tube of one pitch length (C) Unit-cell geometry used to determine cover factor; x and y are unit-cell height and width, respectively[8].

The traditionally two-dimensional made braided sleeves used in manufacturing conventional McKibben artificial muscles are sourced commercially and manufactured with industrial braiding machines [10]. As shown in Figure 3, the braiding machine assembles multiple individual fibers by using several rotary spools to produce a cylindrical hollow braided sleeve.
Two dimensional-braided sleeves are structurally divided into three categories. Biaxial-braided sleeve is the most widely used braid structure in industrial textiles, especially in the composite industry. A single yarn set are (generally orientated at an angle in the + θ and - θ directions) interlacing with each other around mandrel to form the braided fabric surface as shown schematically in Figure 2A. This structure, however, suffers from poor impact resistance because of crimp and low delamination strength due to the lack of binder fibers in the thickness. Triaxial-braided fabric normally consists of three sets of yarns and intertwine with each other around the axial yarns at about 45° angle as shown in Figure 2B. In this method, braiding very dense structure patterns is less feasible compared to biaxial-braided fabrics. Although the axial directional properties are improved in this method (Figure 4). Currently, various types of braids, made of nylon, polyester and carbon fibers are commercially available providing different advantages and disadvantages to the performance of the McKibben muscles.
Lab-scale braiding machines, however, suffer from several essential disadvantages. Firstly, the braiding machines are limited in generating only a narrow range of braid angles, where the braiding angle α is the angle between the longitudinal direction of the braided sleeve and the fibers that are helically wrapped to form the braid. Commercially available braids have a limited selection of braid angles typically in the range of 15o- 35o. Secondly, producing a consistent cover factor is limited due to the friction between fibers. The cover factor is defined as the ratio of area occupied by fibers to the total braid surface area and is a function of braid diameter, initial braid angle, fiber width, and the number of threads. Again, the variation in cover factor from commercially available braids is limited and most have a cover factor in excess of 85%. Third, long fiber lengths are needed to operate braiding machines, which limit the introduction of novel fiber materials for research-scale production especially when only short lengths of experimental fibers are available.
Smart Birded Sleeves for Contraction Sensing
Using traditional or prismatic joints is generally required to precisely measure the motion of Mckibben muscles. Particularly in robotic applications using the Mckibben muscle with sensors is a normal practice to allow for closed-loop control of the generated motions. Research [11,12] has shown that measuring the motion is possible by using smart braided sleeves in manufacturing the McKibben muscles. The traditional braided sleeves of a pneumatic artificial muscle (PAM or McKibben muscle) were interlacing with conductive, insulated wires. Ultra-flexible wires with soft copper stranding and PVC insulations were utilized as conductive wires. This particular braid was assembled with 16 helices equally woven to the right and left directions. These wires acted as a solenoid-like circuit with an inductance that more than doubles over the PAM contraction. Following the actuator contraction, the direction of conductive fibers become more aligned therefore the inductance of the circuit increases. Figure 5 shows the schematic view of the smart braided sleeves used in manufacturing McKibben muscles.
In this study, three structurally different braids were assembled to match the mathematical models. As shown in Figure 6 the authors modeled the inductance of the smart braid with either a simple long solenoid
a) or by using the Neumann formula on 16 helices
b) that are radially distributed about the actuator and electrically connected in series. The results then were compared with measurements from a smart braid stretched over dowels of different diameter
c) 4. Electrically conductive braided sleeves Conductive braided sleeves were used to manufactured miniature and bladderless McKibben artificial muscles [5]. As shown in Figure 7 the conductive braids were assembled with scale lab braiding machine using cotton fibers and steel wire in a parallel direction.
The resistivity of the conductive braid was reported to be ∼18 Ω. As mentioned earlier the cover factor of the braided sleeve is an important parameter and should be closely monitored the braid manufacturing process. In this study, the conductive braided sleeve was manufactured with different cover factors by independently decreasing the diameter of the braid yarn. The ultimate aim of this study was to keep the thermo-sensitive material (paraffin) inside the braided sleeve without using any inner bladder. The thermossensitive material was used to generate a sufficient pressure inside the conductive braided sleeve similar to air in pneumatic version. Adequate conductivity was required to electrically stimulate the thermos-sensitive material and consequently activate the muscle.
To manufacture the bladderless McKibben muscles, researches used the principles of breakthrough pressure [13]. The pressure needed to push a non-wetting liquid through the pores of a membrane is called the breakthrough pressure, P, and is related to the membrane and liquid properties by the following Young–Laplace equation where, r, is radius of the pores, σ and θ are the surface tension of the liquid and the contact angle, respectively. As shown in equation 2, for any pair of materials, the breakthrough pressure increase as the size of pores decreases. Pore sizes in a braid can be expressed in terms of the cover factor, C, which was defined earlier
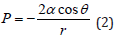
The muscle made of the conductive braided sleeve with the cover factor and average pore size of 0.73 and 0.27 mm was able to prevent the wax exuding through the pores during the actuation tests for many cycles. Figure 8 illustrates the microscopy images of two conductive braided sleeves with different cover factors packed with a thermos-sensitive material.
Figure 8: Microscopy images of conductive braided sleeves with high (A) and low (B) cover factors packed with thermossensitive materials (C and D). (E) the Entire conductive bladderless McKibben muscle[5].
Three-Dimensional Printed Braided Sleeve
An alternative method was investigated to manufacture braided sleeves using a three-dimensional (3D) printing technique [14]. 3D printing method was chosen to achieve more versatility in controlling the geometry and the structure of the braids. This unique 3D printing technique is simple, fast, and accurate that can be easily modified to fabricate tools for small robotic systems where custom manufacturing is required. The braided sleeves in this study were made by employing an extrusion style threedimensional (3D) printing machine using a similar technique to that introduced recently. Each individual printed line was made of polycaprolactone (PCL) material and was precisely printed around a rotating cylindrical steel rod. An additional advantage of this method was the ability to incorporate the hydraulic end connectors directly into the braided sleeve structure. The end connectors are an integral part of the McKibben muscle system and achieving leak-free connection to the hydraulic fluid supply and robust mechanical connection to external loads is a challenge that can be uniquely addressed using 3D printing. As shown in Figure 9, the manufacturing process of 3D printed braids is a follow. The right to left printing direction was first performed as described above and then the entire mandrel with the printed helix was dip- coated in alginate solution and dried. The left to right printing direction was performed to form the second helical fiber on top of the dry alginate film. The mandrel was then immersed in the water bath to dissolve the alginate interlayer. By removing the alginate films from between the PCL helices the double-helix braids with disconnected fiber crossover points were successfully produced. The braided sleeves were then removed from the steel mandrel. The cover factor was constant at 0.47.
As shown in Figure 10C, the printed braids have integrated end connectors to simplify the assembly of the completed McKibben muscle. The effect of fiber connection in crossover points has been investigated. In this particular study, it has been found that the braided sleeves with connected fibers were unable to produce any actuation due to mechanical failure of the fibers (Figure 10A & 10B). Future directions in the future, it would be worthwhile to three-dimensionally print the braided sleeve using conductive materials. It would be then feasible to manufacture braided sleeves which contain conductive and non-conductive helices similar to those explained in sections 3 and 4 and pave the way for entirely printing the braided sleeves for in situ strain sensing applications. This task can be done via using conductive polymer composites with adequate viscosity for 3D printing applications.
Figure 9: (A) Photograph of printing set for manufacturing polymeric braided sleeve (B) Schematic illustration of the manufacturing process of 3D printed braids. All the manufacturing steps shown in the figure have been conducted around a mandrel[14].
Figure 10: Illustration of the deformed shape of one junction point unit (A) connected junction point before (blue ribbons) and after (red dotted lines) pressurization (B) disconnected junction point before (blue ribbons) and after (red dotted lines) pressurization (C) The entire McKibben muscles manufactured with 3D printed sleeve[14].
No comments:
Post a Comment
Note: Only a member of this blog may post a comment.